
General Description
A general description of the fixed prototype developed was provided in The CLEAN Fixed Monitoring Prototype. The following guide provides a more detailed description of the deployment and interconnection of the hardware elements that compose the fixed measurement system, which you can see in Figure 1.
Figures 2 and 4 show the sensing block, which is the fundamental part of the whole system. It contains the sensing chamber, the array of sensors, and the microcontroller as described in The CLEAN Fixed Monitoring Prototype. Figure 2 shows an internal view of the chamber and the sensors, while Figure 4 shows an internal view of the hardware components. The diagram in Figure 3 illustrates the different subblocks and components of the system, which will be described next with more detail.
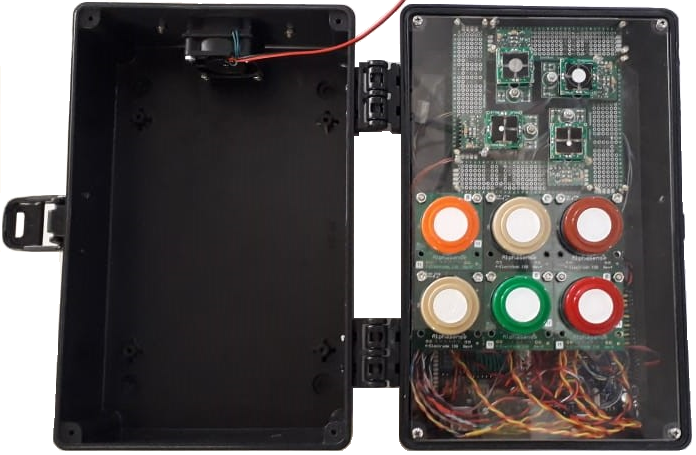

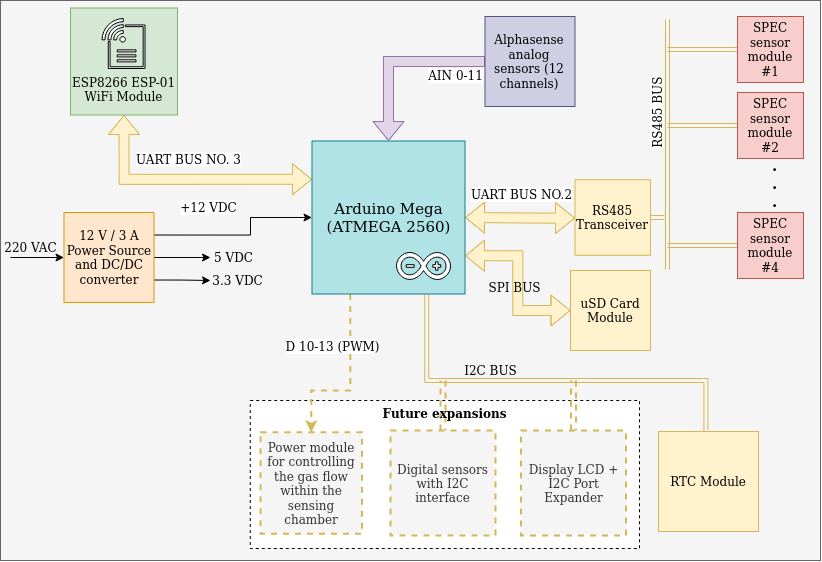
The sensing chamber
The sensing chamber is the system component that contains the sensors, the gas transportation system, and the microcontroller blocks. It is within this chamber that the sampling process takes place.
Figure 5 shows separately the Sensing Chamber components and their location on the prototype which are:
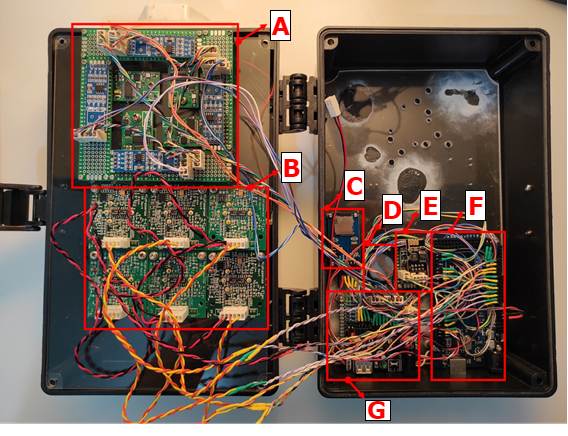
A) Arrangement of sensors “SPEC sensors”;
B) “AlphaSense” sensor array;
C) SD Card module;
D) RTC module;
E) Wi-Fi module;
F) Arduino MEGA 2560;
G) Voltage regulator
An air transportation system, consisting of two 12 VDC cooler fans, collects the gas samples from the ambient air into the chamber. Figure 6 illustrates the direction of the gas flow within the sensing chamber. The inlet consists of a 50 mm diameter flange (which is used for coupling with the external parts of the sampling system) and a filtering screen.

Figure 7 shows the inlet and the outlet of the chamber respectively. The sampling volume inside the chamber and the position of the coolers are shown in Figure 8. The dimensions of the coolers were 40x40mm, and they were fixed with four screws M2x30mm with a nut and washer. Inside the volume of the chamber, the surfaces of the gas sensors interact with the gaseous components and produce a response signal proportional to the gas concentration.

A) Outflow Gases;
B) (9-14)V Power Source Standard P4 Connector;
C) Data Connector “Standard USB-B)”;
D) Gas Entrance.

Equipment Assembly
The equipment assembled and installed in the field can be verified in Figures 9 and 10. The outer box is the environmental box model Atlantic 352 00 from Cemar & Legrand with IP66 protection level.

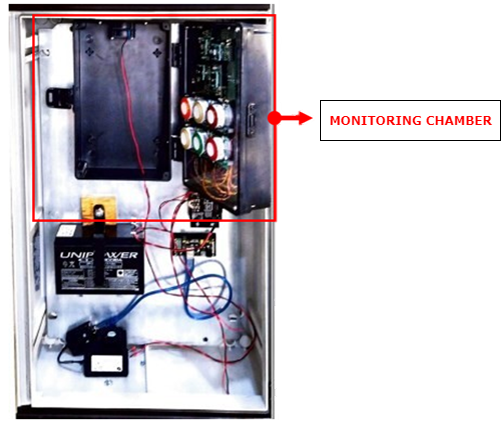
Table 1 below summarizes the list of materials and their quantity, description, characteristics, and illustrative pictures to assemble the outer box.
Qnt | Item | Description | Characteristics | Ilustrative Picture |
1 | Plastic box | Switchboard IP66-IK10RAL7035 | Internal measures 00 x 00 x 00 | ![]() |
1 | PVC Pipte | PVC Pipe for air collector duct | Diameter 50 mm, length 610 mm | ![]() |
1 | Ventilation Terminal | Diameter 50 mm | ![]() | |
1 | PVC Flange | 50 mm PVC Pipe flange | Diameter 50 mm | ![]() |
1 | Threaded sleeve | 50 mm for 1 x 1/4″ | Connected to the pipe follower coming out if the threaded sleeve. It is threaded into the sensor box | ![]() |
1 | Threaded sleeve | 50 mm | Connected to 50 mm flange | ![]() |
Table 1. List of materials for assembling the outer box
The sensors
The monitoring system can take two sensing types with distinct technology which can be chosen by the user accordingly to the needs and application of each project. This manual will be dealing with both arrangements.
Table 2 describes all the necessary components to assemble the sensors arrangements from SPEC senor and AlphaSense.
Required materials and components list
The required materials and components list to assemble the gas reception and exhaust part of the sensor chamber or measuring is shown in Table 2
Qnt | Item | Description | Illustrative Picutre |
1 | CO-B4 | Carbon Monoxide Alphasense Sensor | ![]() |
1 | H2S-B4 | Hydrogen Sulfide Alphasense Sensor | ![]() |
1 | SO2-B4 | Sulfur Dioxide Alphasense Sensor | ![]() |
1 | NO-B4 | Nitric Oxide Alphasense Sensor | ![]() |
1 | NO2-B43F | Nitrogen Dioxide Alphasense Sensor | ![]() |
1 | OX-B431 | Ozone Alphasense Sensor | ![]() |
1 | NH3-B1 | Ammonia Alphasense Sensor | ![]() |
3 | CO/H2S/SO2 4-electrodes ISB | Individual Sensor Board for B4-Series Alphasense sensors for measuring CO/H2S/SO, with connector | ![]() |
1 | NO 4-electrodes ISB | Individual Sensor Board for B4-Series Alphasense sensors for measuring NO, with connector | ![]() |
1 | NO2/O3 4-electrodes ISB | Individual Sensor Board for B4-Series Alphasense sensors for measuring NO2/O3, with conector | ![]() |
1 | NH3 4-electrodes ISB | Individual Sensor Board for B4-Series Alphasense sensors for measuring NH3, with connector | ![]() |
1 | O3 Spec Sensor | O3 Spec Sensor for IoT, model DGS-O3-968-042_9-6-17 | ![]() |
1 | SO2 Spec Sensor | SO2 Spec Sensor for IoT, model DGS-SO2-968-038 | ![]() |
1 | NO2 Spec Sensor | NO2 Spec Sensor for IoT, model DGS-NO2-968-043-9-6-17 | ![]() |
1 | CO Spec Sensors: DGS-CO-968-034 | CO Spec Sensor for IoT, model DGS-CO-968-034 | ![]() |
5 | MAX487 | RS-485 transceiver module | ![]() |
8 | Spacers | Spacers MS*10+4 to Tinned Universal Breadboard With screws | ![]() |
6 | Conector MOLEX | Conector MOLEX 4 pins | ![]() |
9 | Connector MOLEX | Connector MOLEX 2 pins | ![]() |
5 | Breadboards | PCB Tinned Universal Breadboard 2x8cm | ![]() |
Table 2. List of components and materials for assembling the sensor chamber gas exhaust and reception.
Fixing the Sensor Array in the measuring Chamber
An acrylic board is necessary for fixing the sensors in the right way and isolating the gas chamber from the hardware spot. This is demonstrated in Figures 11, 12, and 13. The project for manufacturing the acrylic board is contained in the project’s documentation, which can be modified according to your needs.
Figure 11 shows how the sensor’s fixation is done on the acrylic board, with 2.5×5 mm screws with nuts. The sensor is embedded at the ISB board in a simple way as shown in Figure 12.
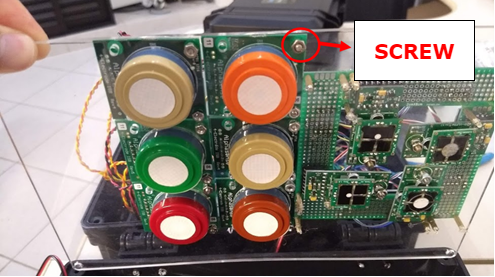
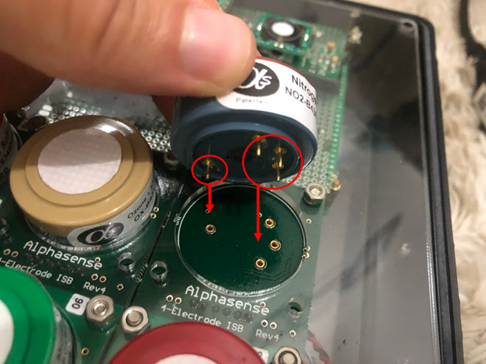
Figure 12. The fit place of the sensors at ISB board.
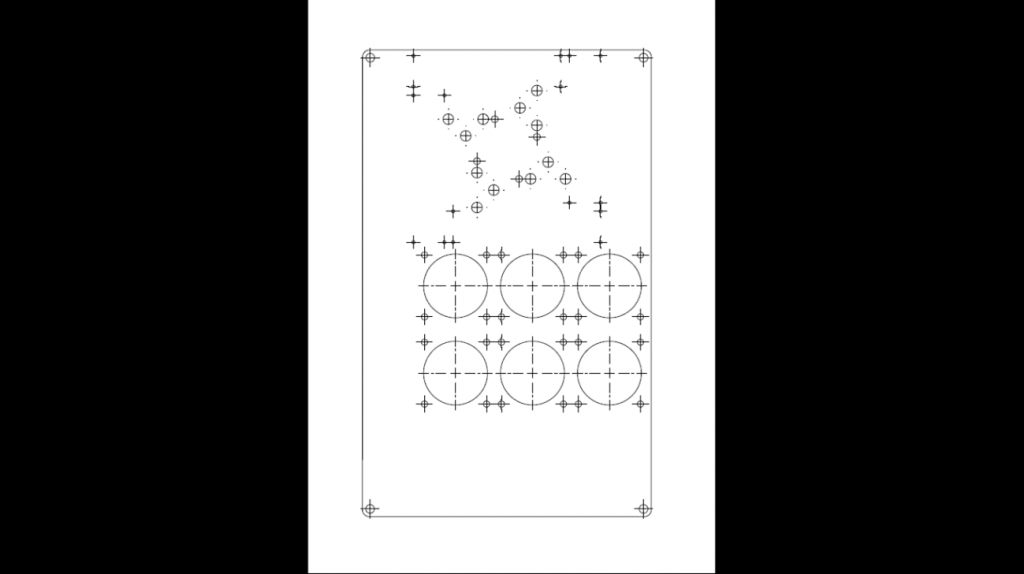
Figure 13. Acrylic board schematic.
Alphasense Sensors Array
Table 2 contains the necessary items to assemble the AlphaSense sensor’s arrangement. After the correct sensor’s arrangement and the other internal hardware components from monitoring chamber, you can forward assembling, making the electrical connection of communication and power supply of the set of sensors.
The connections can be done with the 0.2mm² section wire, welding “headers” at the tips, isolating them correctly with a heat shrink duct. The wire tip which will be connected to the sensor board ISB’s connector must be isolated at the connector itself which comes with the ISB board.
Figure 14 shows the wiring diagram of the electrical supply of the sensor arrangement and Figure 15 shows the communication wiring diagram.

Figure 14. Electrical supply connection diagram for the AlphaSense sensor array.

Figure 15. Communication wiring diagram of the AlphaSense sensor array.
The following table shows which Arduino ATMEGA 2560 pin is connected to each Alpha Sense sensor.
Sensor Pin | Arduino Pin |
VIN+ | 5V |
VIN- | GND |
OP1- | GND |
OP2- | GND |
OP2 + (Sensor NO2-B43F ISB) | A0 |
OP1 + ( Sensor NO2-B43F ISB ) | A1 |
OP2 + (Sensor SO2 – B4 ISB) | A2 |
OP1 + (Sensor SO2 – B4 ISB) | A3 |
OP2 + (Sensor CO – B4 ISB) | A4 |
OP1 + (Sensor CO – B4 ISB) | A5 |
OP2 + (Sensor OX – B431 IAB) | A6 |
OP1 + (Sensor OX – B431 IAB) | A7 |
OP2 + (Sensor H2S – B4 ISB) | A8 |
OP1 + (Sensor H2S – B4 ISB) | A9 |
OP2 + (Sensor OX – B431 ISB) | A10 |
OP1 + (Sensor OX – B431 ISB) | A11 |
Table 3. Connections between Arduino ATMEGA 2560 and Alpha Sense Sensors
Array of SPEC sensors
The fixation of the sensor’s arrangement from the SPEC sensor is done through the PCB Tinned Universal Breadboard handily made. This board is equipped with female “headers” to which the sensors are connected. At this same Tinned Universal Breadboard are also installed the transceivers. The PCB Tinned Universal Breadboard is fixed directly at the acrylic board between the M2*10+4 spacers. The electric and data connection between the Tinned Universal Breadboard is done through the MOLEX connectors.
Figure 16 presents the connection details of the SPEC Sensor’s sensor at the dedicated board: Figure 17 presents the bottom view of the sensors arrangement, detailing the 2.5x5mm fixation screws.
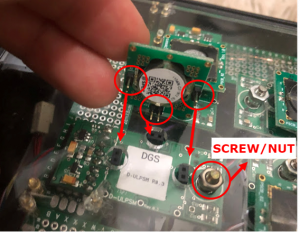
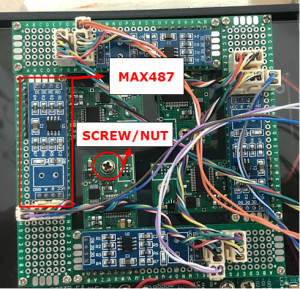
Figure 18, shows the Tinned Universal Breadboard side view which shows the fixation spacers, headers, a MAX487, and the MOLEX connectors utilized. The spacers are threaded directly into the contained perforation acrylic board design.

Sensor Chamber Power and Communication Connections
The necessary components to assembling the sensor’s chamber hardware items are shown in Table 4.
Qnt | Item | Description | Characteristics | Ilustrative Picture |
1 | Tinned Universal Breadboard | 2 x 8 cm | Board where it is installed the voltage regulator source | ![]() |
1 | Real time clock RTC DS3231 | Module RTC | ![]() | |
1 | ESP8266 ESP-01 | Wi-Fi Serial Module | ![]() | |
1 | Mb102 | 3V and 5V regulator source | ![]() | |
16 | Spacers | M2*10+4 Spacers to Tinned Universal Breadboard with screws | Used to secure circuit components | ![]() |
1 | SD Module | 43MD36 Model | ![]() |
Table 4. List of components for assembling the sensor chamber.
After assembling the sensor array and prefixing the electronic components of the measuring chamber, it will be necessary to make the electrical connection of the power and communication of all components involved in the system. To do that it is used a 0.2mm² section wire or greater for communication and 0.5mm² for power connections. The power supply diagram is shown in Figure 19 and attention must be paid to the parallel connection made between the 12V input of the regulator and the MEGA Arduino. As a strategy to improve the performance of the power supply regulator, a jumper was added and is shown on the power diagram.


The fixing of the components is done by using brass spacers in the same way used in Figure 18 on the assembly of the SPEC Sensor array. To place this spacer, make a 2mm perforation directly in the plastic and screw the spacers directly into this hole.